Production maintenance involves carrying out machinery checks to identify defects that threaten their functionality before undertaking corrective measures where necessary. The manufacturing chain in your company involves the team of operators and the maintenance team working towards common production goals. However, the two teams might get into conflicted positions without sufficient leadership and communication to ensure streamlined activities. It is important to establish a strong relationship between maintenance and production in the establishment to enjoy the following benefits:
Maximum Resource Utilization
Regular equipment at your establishment will improve resource utilization for success in gaining the production goals set. Establishing problematic system operations before the equipment breaks down will ensure that your team handles the problems quickly. The result is that there will be little downtime from total breakdowns where extensive maintenance steps will be necessary. Regular checks and maintenance eliminate the risk of suffering long periods of machine downtime during which production will not occur. Prioritized maintenance will maintain the equipment with critical problems while those with minor problems continue operating.
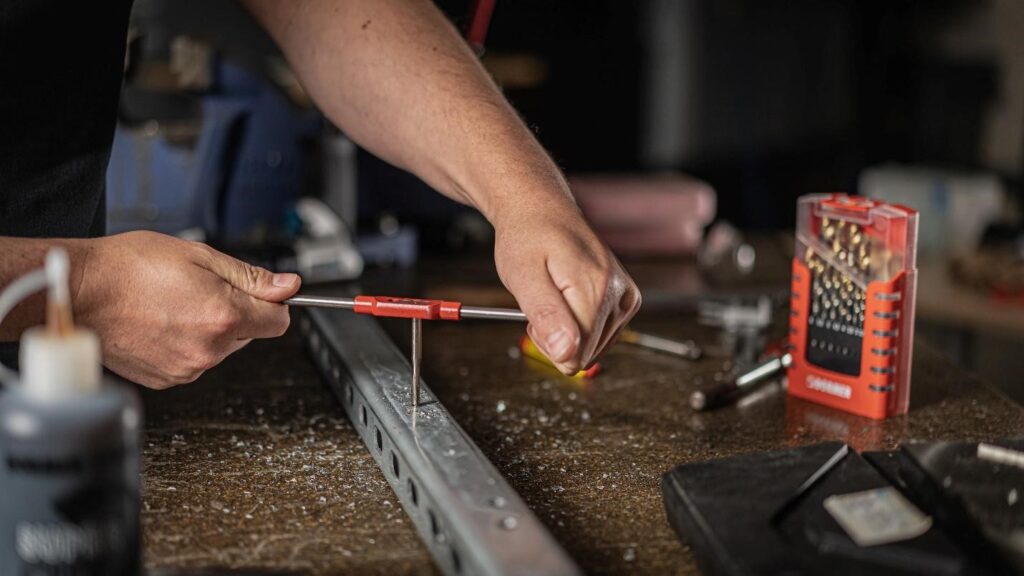
Resource utilization from employee productivity is also a viable reason to encourage regular maintenance. The employees depend on working schedules to ensure they cover their workloads for smooth operations during production. However, unpredicted equipment failures leading to extensive downtime will take away the facilities that enable employee productivity. The result is that you will be paying the workers for unaccomplished work, making it a waste of the scarce resource that is labor. Regular maintenance practices will ensure short and scheduled downtime during which other plans will be in place.
Streamlined Teamwork between Different Departments
The running of the production processes in the company relies on the at least three departments working together in harmony. The operators ensure that the production functionalities run as expected, while the maintenance team ensures that equipment work at optimal levels. The management team oversees the two teams to enable sufficient communication and coordination to achieve production objectives. The managers in your establishment must create a common ground for the maintenance of machinery without impeding the production expectations of the operators.
Scheduled maintenance activities after sufficient coordination will ensure that each department adjusts its activities accordingly. The constant communication enables a clear strategy that will allow the maintenance team and operators to carry out their mandate. Maintenance prioritization is a strategy that allows operators to work with equipment at less risk of breakdown while the ones at high risk undergo maintenance. The outcome is employee satisfaction with zero chance for conflicts in the workplace.
Opportunity for Employee Training
The scheduled maintenance activities present a period when operators will have a lot of free time due to downtime with some equipment. The management team can use the opportunity to allow the operators a chance to observe the maintenance experts’ work to restore optimal machine functionality. The operators will learn about essential equipment elements to help them make better decisions to ensure a high productivity level.
The feedback from the operators about the operation characteristics observed from the machines will help the maintenance team identify the defects quickly. The coordination between the two teams during maintenance will better understand the problem and reduce downtime by quickly resolving the issue. The know-how about equipment care gained by the operators will also put them in a position to handle them better, thus ensuring longer machine lifespans.
Improved Production Strategies
The occurrence of regular equipment maintenance allows the teams to analyze their production strategies repeatedly. The conclusions drawn from the routine analysis will provide guidelines that the management can use as lessons to create improved production strategies in the future. The manufacturing sector is a field that is changing with time; thus, new methods will arise to enable higher productivity with available resources. Coordination between operators and maintenance experts will allow the teams to identify areas where changes will positively influence the final product creation.
One lesson the teams can draw from the maintenance activities is the impact of particular processes on the equipment. Adjusting the processes allows the experts to conclude about equipment response to various equipment compared to the resulting productivity levels. It is possible to create new strategies that are less damaging to the machines while maintaining the quality of products. The new production strategies should match the customer needs that keep evolving to ensure customer satisfaction.
Reduced Production Costs
The cost of production depends on the efficiency of the equipment relative to the resources used. The cost of raw materials, employee salaries, and equipment purchase, maintenance, and repair require compensation from product sales to realize revenues. Production costs go up when the company encounters cases of equipment downtime due to dysfunctional machines that derail production activities. The company will be investing in salaries and materials while the low production during downtime affects the sales since the product numbers and quality reduces.
However, regular equipment maintenance reduces production costs in a few ways. First, the low downtime is a sure way to enable optimal product creation and thus maintain a stable revenue flow from the sales. The extra revenue covers any costs that go into production, thus ensuring continuity in company profits for the long term. Maintenance improves employee satisfaction and focuses on equipment efficiency instead of production deadlines. The result is that the extended machine lifespans save the company money required to acquire new equipment or pay for repairs after a total breakdown.
The benefits of regular production maintenance in a company come from the proactive nature of the measures involved. The process relies on careful performance analysis of different equipment to gauge their functionality during different production procedures. Differences in the production capabilities determine the machines that will receive priority maintenance to allow a continuous processing workflow. The scheduled maintenance creates predicted downtime periods during which employee attention is redirected to other activities that contribute to the realization of company objectives. The danger of wasting company resources during unpredicted downtime is less since the equipment does not deteriorate to a breakdown level.
Leave a Comment
You must be logged in to post a comment.