Implementing the right finishing technique will enhance your product, durability aesthetics, and strength said Dr. Shahid Rizwan, who is the production department head of Germen based manufacturing firm. With the advancement of rapid prototyping and Industry 5.0, the market competition is increasing day by day. The industry owners must compete in this rapidly growing market if they want to stay in the game. Choosing an appropriate, sheet metal finishing option for custom metal machining will not only boost your product quality, but they also make your product look aesthetic and bring loyal customers to you.
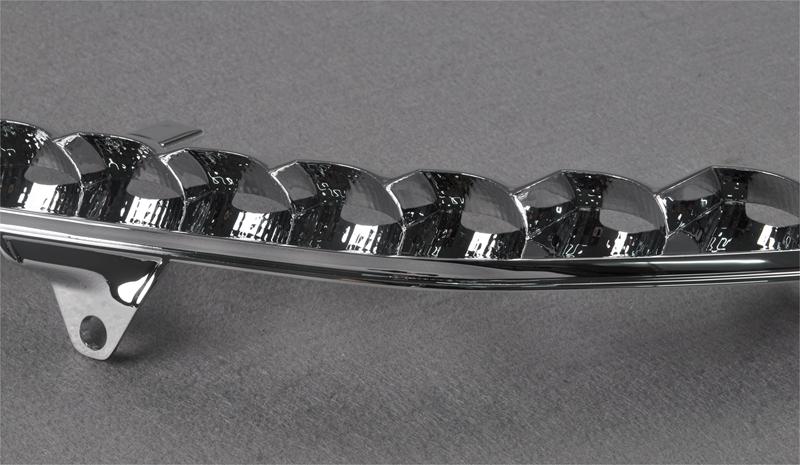
However, choosing a finishing technique without knowing the design and material considerations will affect your production. So before making any decision, one should be well aware of all the parameters. Further, in this article, we will discuss the top considerations for choosing an appropriate, sheet metal finishing option for your business. So, stay with us to boost your production.
Coating Versatility
With the availability of a lot of coating versatility in the market, choosing the right one is a difficult task. An expert engineer is always required, as the coating is implemented as per the usage of the products. Every technique provides unique features such as color, aesthetics, durability, and toughness. Here we discuss some techniques that are implemented and why are the best sheet metal finishing considerations.
- Powder Coating
Powder coating is a way to finish sheet metal parts. This technique provides aesthetic looks with long-lasting durability. It provides a range of colors and textures making it perfect for applications where visual appeal is important. Moreover, powder coating prevents chipping, and its ideal for parts that are exposed to rough environments, as it prevents wear and tear and increases durability.
- Anodizing
Anodizing is a method that produces a layer, on metal surfaces shielding them from corrosion. This makes it perfect for sheet metal components that come into contact with moisture or extreme conditions. Apart, from providing protection anodized coatings also add a touch to the surface by offering different colors and finishes. This not only enhances its functionality. But it also boosts its overall aesthetic appeal.
- Electroplating
Electroplating is a process where a layer of metal is applied onto the surface of the sheet metal component. This technique provides protection, against corrosion. Can also improve the overall aesthetic appeal making it a widely preferred option, for decorative purposes.
- Paint and Liquid Coatings
These coatings provide a broad spectrum of colors and finishes, making them suitable for a variety of applications. They are often used when a specific color or texture is required.
The selection of a coating should depend on how the sheet metal part will be used and the environmental factors it will face. Coatings that offer versatility can cater to applications offering both practicality and visual appeal.
Material Compatibility
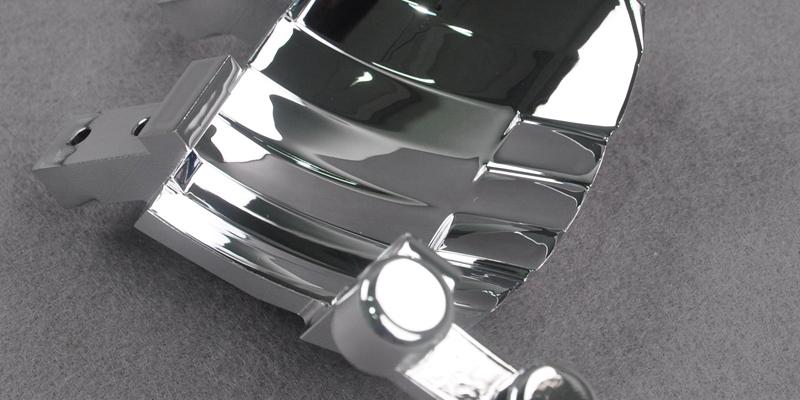
Choosing the finishing option is essential, for maintaining the quality and durability of sheet metal parts. Each type of metal, like steel, aluminum, and copper has its characteristics and reacts differently to coatings. There are factors to consider for sheet metal finishing
Galvanic Corrosion
Galvanic corrosion is a phenomenon that occurs when different types of metals come into contact leading to one metal corroding, than the other. To prevent this process and ensure the durability of sheet metal parts it is essential to choose a surface treatment that matches the base metal thereby avoiding galvanic corrosion.
Adhesion
Applying appropriate adhesion is the most important aspect of sheet metal finishing. During the finishing process, it should be carefully inspected that the surface finishing materials are properly attached to the product.
This practice will definitely increase the product’s durability and toughness. The bond between the coating and the metal surface is totally dependent upon the adhesive used. so, it’s the most important factor that decides the product’s long-lasting characteristics.
Temperature Resistance
Some finishing options may not withstand high temperatures or extreme temperature fluctuations. Ensure that the chosen finish can endure the environmental conditions to which the sheet metal part will be exposed.
Corrosion Protection
Corrosion protection is a significant concern for sheet metal parts, particularly those used in outdoor or corrosive environments. The choice of finishing option plays a vital role in preventing corrosion and extending the lifespan of the parts. Anodizing, galvanizing, and specific paint coatings are examples of finishes that offer excellent corrosion resistance.
Consider the following factors when evaluating corrosion protection
Exposure
The most important factor before deciding on a sheet metal finishing technique is to analyze the part’s operational conditions. For example, if the parts are exposed to too many harsh conditions, then they should be high-quality surface finishing techniques.
Maintenance
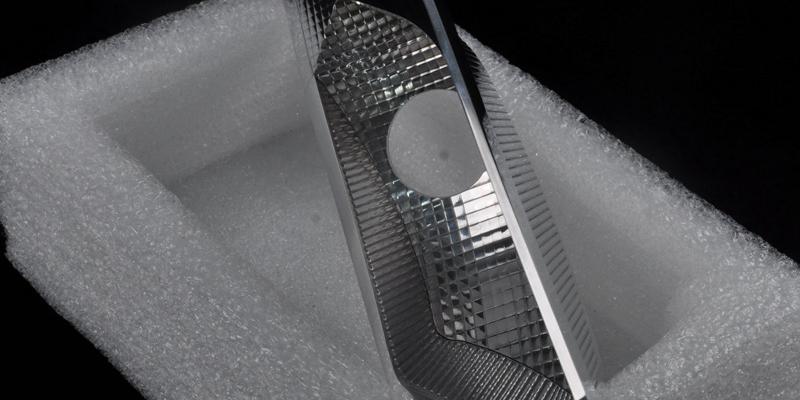
Some finishes may require periodic maintenance to retain their corrosion resistance—factor in the ongoing care and associated costs when selecting a finish.
Budget
Corrosion-resistant finishes often come at a higher cost. Balancing the level of protection with the available budget is an important consideration.
Conclusion
If you are an industry owner then you will definitely know the importance of sheet metal finishing. But after reading you are well aware of the fact that It’s crucial to consider factors like the versatility of coatings, compatibility with materials, and protection against corrosion for smooth custom metal machining.
These aspects significantly influence the performance and durability of the parts. By giving thought to these factors, you can ensure that your sheet metal parts meet all the functional, aesthetic, and durability requirements, for their intended use.
So, make an informed decision as by applying these techniques in custom metal machining are not only improved aesthetically but also able to withstand various environmental conditions over time.
Leave a Comment
You must be logged in to post a comment.